
PK: In your opinion, are there any specific features or abilities that are necessary to create kurdybans?
You need to have some knowledge, but you absolutely do not need to be, for example, a conservator of monuments.
The most important thing here is manual skills. You also need to have a lot of patience, because this activity requires great precision and the whole process is incredibly time-consuming.
I think the challenge may be the fact that with this work, you have to put your artistic ambitions aside a bit. You have to remember that it's not about painting what you want - you have to take into account that, for example, the entire wall must be painted identically. It takes a lot of discipline and humility.
PK: What were the beginnings of your studio?
The kurdybanów workshop has been operating since 2012, but previously it was a conservation workshop. Such a milestone for us was the kurdybanów project made in 2014 for a wine cellar in Gdańsk.
PK: Many people probably don't know what kurdybans are, so who are your customers?
At one point, we managed to complete a large order. This helped a lot of people find out about us. Since then, the studio has been operating continuously and constantly developing.
Now many people also learn about us from social media. It happens that people see our works somewhere on the Internet and then visit us in the studio.

PK: Do you remember your first clients?
The first, really first customers were single people. People who already knew what kurdyban was. Most of them were people from the artistic and design industries. At some point, we were approached by a designer from Gdańsk who asked us to design a curtain for a wine cellar. This was our first large order, thanks to which many people learned about our studio.
I also remember that some time later, a man approached us who was dealing with an "artistic vision" of a certain sanctuary. It was a parishioner there. He decided that the niche in which the statue of Our Lady stands should be covered with curtains. It was quite a demanding project, and we didn't have that much experience yet and initially we were afraid that some complications might arise. Fortunately, everything worked out.
The third and largest client at that time was the Wierzynek restaurant. For those who don't know, this is an iconic Polish restaurant in Krakow, whose history dates back to the 14th century.
I remember the phone call regarding this matter, it stuck in my mind. They were then looking for a contractor because they had already decided that the interior should be decorated with a curtain. They were very happy when we told them that our studio was located in Krakow and everything would be created locally.
As a studio, we created curtains for them from over 150 leathers, which decorated the rooms inside the restaurant. We made more of them, just to stock up. It was a great challenge, probably the biggest so far.

PK: Why was this project such a challenge?
Back then we didn't have the equipment we have now. We use a press to create curtains. At that time it was small, so we had to engage some people to help.
The size of the decorative panels was also a big challenge. To cover the entire wall with curtains, it was necessary to combine individual pieces of skin into a large sheet and then put them on a loom. These were very large elements, over 3 meters high. Since leather is a natural material and reacts to climate changes, with such large dimensions, an improperly installed curtain could become sagging or crack in response to changes in temperature or humidity in the room. To prevent this, we had to use special, custom-made aluminum looms. These were self-tensioning looms, based on a system of springs, thanks to which they adapt to how the leather reacts to the climate. They expand and contract together with the curtain, preventing it from being damaged.
Another size problem was the fact that all the elements had to be assembled on site. It was not possible to assemble them in advance and then bring them into the premises because they simply would not fit.
As part of the project, two large paintings from kurdyban were also created. One of them was an illustration of the legend of the Wawel Dragon. The second one depicted a genre scene - a view of the Krakow market square. Their creation required us to create many matrices representing specific elements. And so on… Overall, it was a long and complicated process. Definitely our biggest challenge.
PK: How long did the implementation take?
The whole project lasted from February to August 2015.
PK: What exactly was created as part of this project?
The entire project consisted of curtains for the so-called Wierzynek Room and the two paintings mentioned above, which were placed in another room. The pattern used on the decorative panels has been specially modified to refer to the so-called motifs. "Wirey Birds". We have also created a special pattern and matrix, made to order for the restaurant - this is a pattern that is registered by the Wierzynek restaurant and can only be used there.
PK: These are clients you have worked with some time ago. Who are your customers today?
We work for both individual clients and museums and cultural institutions. For the latter, we usually make replicas of curtains or replace their missing parts.
However, single people constitute the vast majority of our clients. Often these are people from really different parts of the world. It happens that we answer the phone in the studio and are asked if we are in the studio that day because someone will be traveling to Krakow and wants to visit us. Recently we received such a call from a potential client from Texas.
Many of our current clients are also people who previously came to us to renovate old furniture or objects, including items with curtain elements. These customers often come back to us later to buy kurdyban.

PK: What does working with a client and the process of purchasing a kurdyban look like in your studio?
It depends on whether the customer wants a ready-made product or wants to place an individual, perhaps more complicated order.
Typically, customers call first. Sometimes they also visit us in the studio. Very often, customers do not know exactly what they want. We want to emphasize here that this is absolutely fine. You can come to us with your own idea, but also when you don't have one. Kurdyban may be an interesting choice for an exclusive gift, and we are always happy to talk and present various possibilities. I must admit that when clients come to our studio, ideas usually emerge quickly. Once we have a specific idea, we move on to discussing the details and implementation time.
Currently, our main method of operation is direct work with the client. We plan to open our online store soon, then this process may evolve a bit.
PK: How long does the process of creating one curtain usually take?
It depends, usually it takes about a year to create a curtain from start to finish.
PK: What influences the implementation time?
First of all, its size and level of complexity.
The second factor that greatly affects the production time is whether new dies need to be created for such a curtain. If we already have ready-made matrices, we are usually able to create a curtain in 4-5 months. However, if we use a new pattern and have to create a new matrix, this process takes a lot longer.
PK: Can you tell us what the process of creating a kurdyban looks like step by step?
If we create a new pattern, we first need to create a matrix model and then make the matrix.
Once we have the matrix ready, we move on to the leather embossing stage. We import our leather mainly from Italy and Poland. In the production of cordivans, primarily vegetable-tanned leather is used, i.e. without the use of "chemistry". It is also possible to use semi-vegetable tanned leather. Interestingly, when we started our business, importing such vegetable-tanned leather was a big challenge - especially in Poland. Nowadays, perhaps for ecological reasons, dressing leather with plants has become popular again, so this is no longer a problem.
How is such leather embossed?
The leather is hand-embossed. For this purpose, it is moistened and patterns are "scratched" from the matrix using a rounded wooden tool. This is a stage of work that requires a lot of strength because we need to imprint the pattern well in the material. After "scratching" the pattern, special tools are used to emboss leather. Thanks to them, you can properly press the material into the die in order to emboss it. Since the skin is moisturized when making the pattern, it should be allowed to dry after the process is completed. Typically, you wait approximately 24 hours before moving on to the next stage of work.
PK: And what is the next stage?
When the leather dries, we move on to the silvering stage. You can also perform the process of pressing the kurdyban in a different way. If we use semi-vegetable tanned leather, we first silver it and then emboss the pattern.
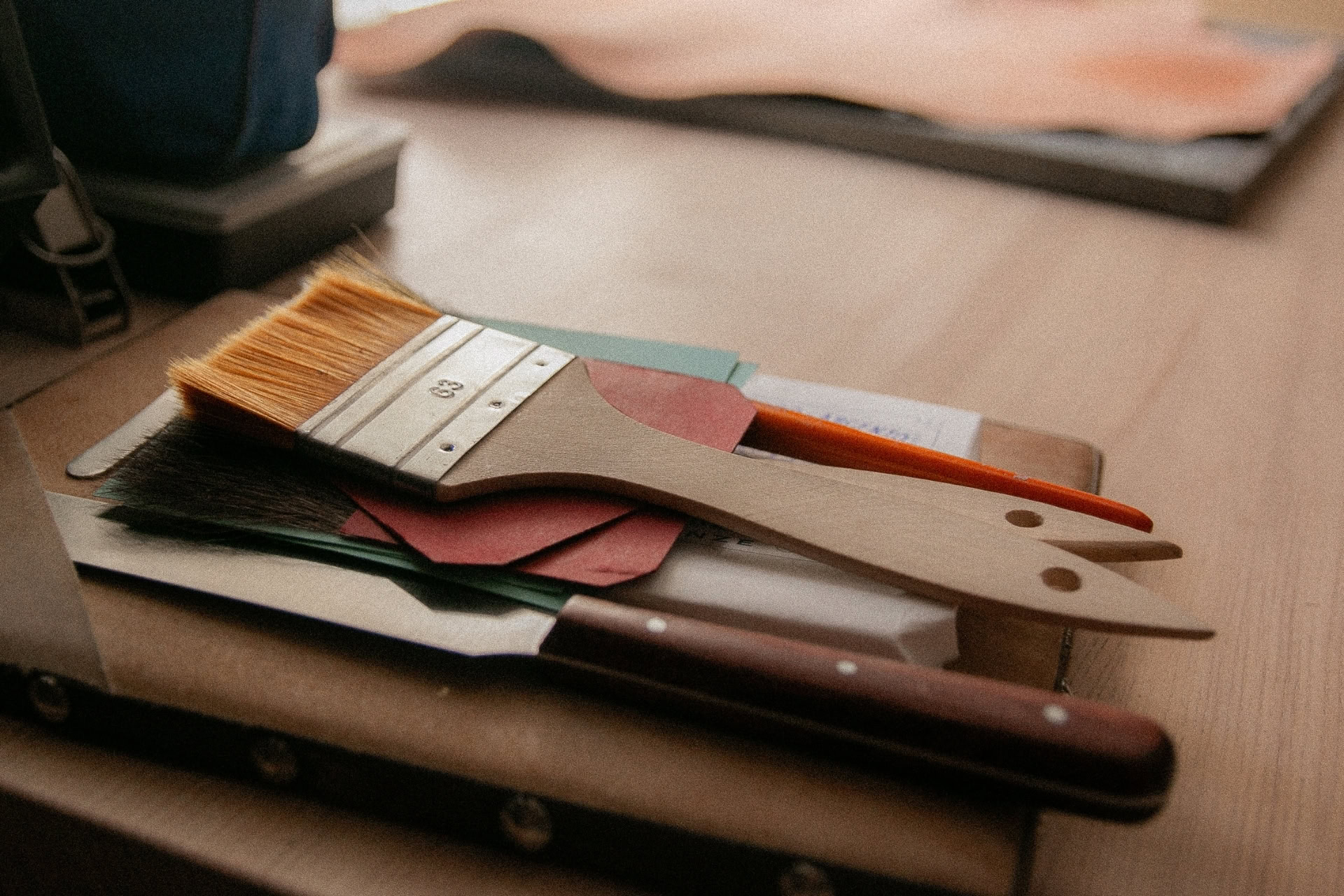
PK: Is this real silver?
Yes, this process involves sticking real silver petals to the skin. A layer of glue is applied to the stretched material, and then gently apply the petal and combine with a brush. After this stage, the metal layer should be protected against corrosion. To this end, you can use beaten egg protein. There are other methods of security. However, the use of protein is an original method that was used at the turn of the 17th and 18th centuries.
After silvering, we can perform punching. Punching involves striking small patterns using a hammer and the so-called punccy. It's a bit like stamping "stamps" on the surface of the skin. Punching is a technique that allows you to decorate both small parts of the curtain and create an entire image. A little curiosity is the fact that the points we use are created by our Dad.
The next stage is varnishing. At this stage, we use a special varnish prepared and cooked by us. It looks like a black, tarry liquid and its smell is not very pleasant. This golden varnish causes the surface of the material to change color from silver to gold. Depending on the project and the client's needs, we adjust the color of the varnish to obtain the appropriate shade.
PK: What happens next?
Then we have to wait a very long time. Typically, if such leather dries out in the summer, when it is quite warm, it takes about 2 months. However, if the temperatures are lower, you have to wait three, four, sometimes even more months before you can start painting on it.
PK: So the next stage is painting the skin?
Yes. After drying, we start painting.
Historically, kurdybans were very colorful. Kurdyban changes and darkens with age, which is why the original kurdybans we see do not reflect the colors they originally had. Many of our kurdybans have slightly more subdued colors because we adapt them to the style with which we now associate kurdybans. Our offer also includes very colorful paintings - for example those based on descriptions of the original colors of historical kurdybans.
When the curtain is painted and we consider it ready, we need to let the paints dry. This again means about a month of waiting.
PK: So after another month of waiting, we finally have our final product?
Basically yes. We just need to think about how we want to display such a curtain. Will it be framed like a painting or hung in a different way, etc.
PK: It is indeed a very time-consuming process. In addition, it uses many expensive raw materials. Will you tell us the cost of the products you create?
The cross -section of our products is quite large due to the characteristics of the object, which is Kurdyban. We offer small items such as bookmarks or other small gifts. The cheapest items cost about PLN 500-600. However, along with the size, complexity and level of personalization of the order, these amounts are growing significantly. Kurdyban prices available immediately are usually around 5 - 10 thousand. PLN, while jewelry decorated with kurdyban usually costs between 4 - 5 thousand. zloty . When we create new matrices for a given client, it can be several thousand zlotys. With such projects there are a lot of variables affecting the final price of the product.
These are definitely niche and luxury products.
Our goal is to popularize kurdybans. We would like them not to be forgotten. We would like there to be people who would want to produce such products.
PK: Your Kurdyban mission has been going on for over 10 years. Has anything changed since you started your studio?
We see a huge increase in interest in smaller Kurdyban items. Such as jewelry, small gifts or wall paintings.
People increasingly come to us looking for, for example, a unique gift for a wedding or anniversary.

PK: How do you see the future of this profession? Is there room for more places like your studio to appear?
There are not many places like our studio. We are the only kurdyban workshop in Poland. This is not a popular activity as the demand for this product is currently quite low. Of course, we would like this to change in the future.
Currently, minimalism still reigns supreme in interior design, but fashion always returns. Perhaps in some time the kurdyban will come back to our interiors.
PK: If this were to happen, are you open to teaching others this craft?
Yes. We already organize workshops and this is something we want to develop.
The main problem is that the path to mastering the technique of making kurdybans is very long. This is a big investment of time.
Unfortunately, the financial barrier to entry into this field is quite high due to the raw materials used. We and our parents were lucky to start this business because our main source of income was historic preservation. I think that if someone set up a kurdyban workshop and wanted to make a living from it from the very beginning, it would be rather unrealistic.

PK: Do you have any advice for young creators and craftsmen
Perseverance is important. You have to be patient and strive for your goal.
PK: Do you have a motto that you follow?
“Don't give up and be ready for anything.”
PK: At the end of our conversation, can you tell us why you think it is worth choosing craft products?
Every craft product is touched by man and paid for by his work. These are unique products. Made from the heart. Typically, a craftsman creates out of love for the material, technique or some idea behind it. Handcrafted products are a connection between humans and humans, without the need for a machine or a computer.
PK: Thank you for the interview
Thank you.