
PK: Having your own designs, you probably started thinking about opening your own studio. What were the beginnings of this studio where we are talking today?
At the beginning, when I opened the studio, it looked like there was only one table and nothing else. A completely empty studio, one table and me sculpting in the middle of it. Sometimes people passed by and you could see them peeping and wondering what was going on, that a guy was sitting in an empty room sculpting something - it must have looked a bit strange.
PK: Well, a lot has changed, now when you pass by you can immediately see what you do.
Yes it's true. Nowadays, it often happens that people pass by and look inside and see chess and me sculpting at the entrance to the studio. Then sometimes they pass by the studio door and after a while they go back and look in again - sometimes they also go inside if they are curious.
PK: What you do is quite an unusual job. Could you tell us a little more about how you learned this craft?
I'm basically self-taught.
Several other people in my family also enjoyed art-related activities. My great-grandfather studied sculpture in Vienna and later in Poland, although he worked as a railwayman, he sculpted as a hobby. I know that he had a small workshop where he carved, for example, eagles, which were later placed in government offices. To this day, you can certainly find his eagles in some offices and fire brigade buildings. My brother, on the other hand, paints pictures. I also like painting, but I'm much better at sculpting.
PK: You mentioned earlier that there were other people in your hometown who dealt with it. Did you also gain knowledge from them?
Yes of course. This also made it easier for me to get started. I had the opportunity to borrow a chisel or learn from them how to sharpen them. Sharpening chisels then turned out to be much more complicated than I thought and the fact that I could gain knowledge in such matters from these people was very helpful.
PK: Is chess carving something you can easily try?
The biggest obstacle here, I think, is the entry barrier - primarily financial. These are not huge amounts, but to try, we need to complete a set of chisels. Good quality wood chisels cost several hundred zlotys. For example, I use about seventeen such chisels to create one set of chess pieces. So this is probably the biggest obstacle, because you have to invest several thousand zlotys to see if we like it and if it makes sense.

PK: Does this make interested people look for a place and people from whom they can learn it?
Yes. Various interested people came here and I sometimes conducted workshops - but during such workshops for beginners, no one picks up such a chisel. This is a very sharp tool that is very dangerous in the hands of an inexperienced person.
PK: This is probably the reason for the character of the master and the feature in craft professions, which probably allows for more controlled learning.
Exactly. This is not something that should be taught by saying "take a chisel and try it, I'll be back in an hour to see the results."
PK: Would you like to share with us what a day is like in your studio?
I usually come here in the morning with a coffee, turn on the lights, put on a wristband and think about what I have to do. If I have something prepared from the previous day, I just sit down and start sculpting. A day when I mainly sculpt goes by very quickly, I don't even know when. This is probably the advantage of doing something that gives us pleasure.
Sometimes there are days when there is less desire to work, or I sculpted for too long the previous day and my wrist hurts, which makes work very difficult. In such situations, I try to find something else to do among the tasks I have to do. Then, for example, I prepare sketches and prototypes of new figurines or paste boxes - there is always something to do, so I don't get bored.
PK: Does he also make cases for storing chess pieces?
The caskets are more of a carpentry job, so I don't make them myself. However, I personalize them to adapt to specific projects.
PK: Coming back to chess pieces, how does carving them differ from carving other objects?
First of all, when we carve chess pieces, we should think about the whole, not a single piece. You must remember that this is a whole set that must be consistent with each other. Visually, the recipient must immediately perceive them as a set and at the same time recognize individual figures. Please remember that these are chess pieces, not just a pretty decoration - they must be not only visually interesting, but also functional.
PK: How do you manage to create so many diverse sets, some of them very unusual, in which you can always easily recognize all the figures?
I try to test the new models I design quite well. I also often take photos and share them, e.g. with friends, asking them to rate the prototypes. It is very important to sometimes turn to someone from outside, because when we look at our own projects for hours, it is often difficult for us to be objective and look at them from the client's perspective.
PK: How time-consuming is the process of creating such a set?
It depends mainly on how many details there are, because this translates greatly into working time. The second issue is, of course, whether I am carving a model that I have already developed and know, or I am working on something completely new - e.g. an individual order. Creating new chess designs is done very slowly because you have to think about each step and test different approaches.
These chess models, which I have been making for a long time, I make much faster. I'm more experienced in them now and I know exactly what I have to do. Then, instead of starting carving with a wooden block, I usually use pre-embossed shapes to work with, which makes it much easier.
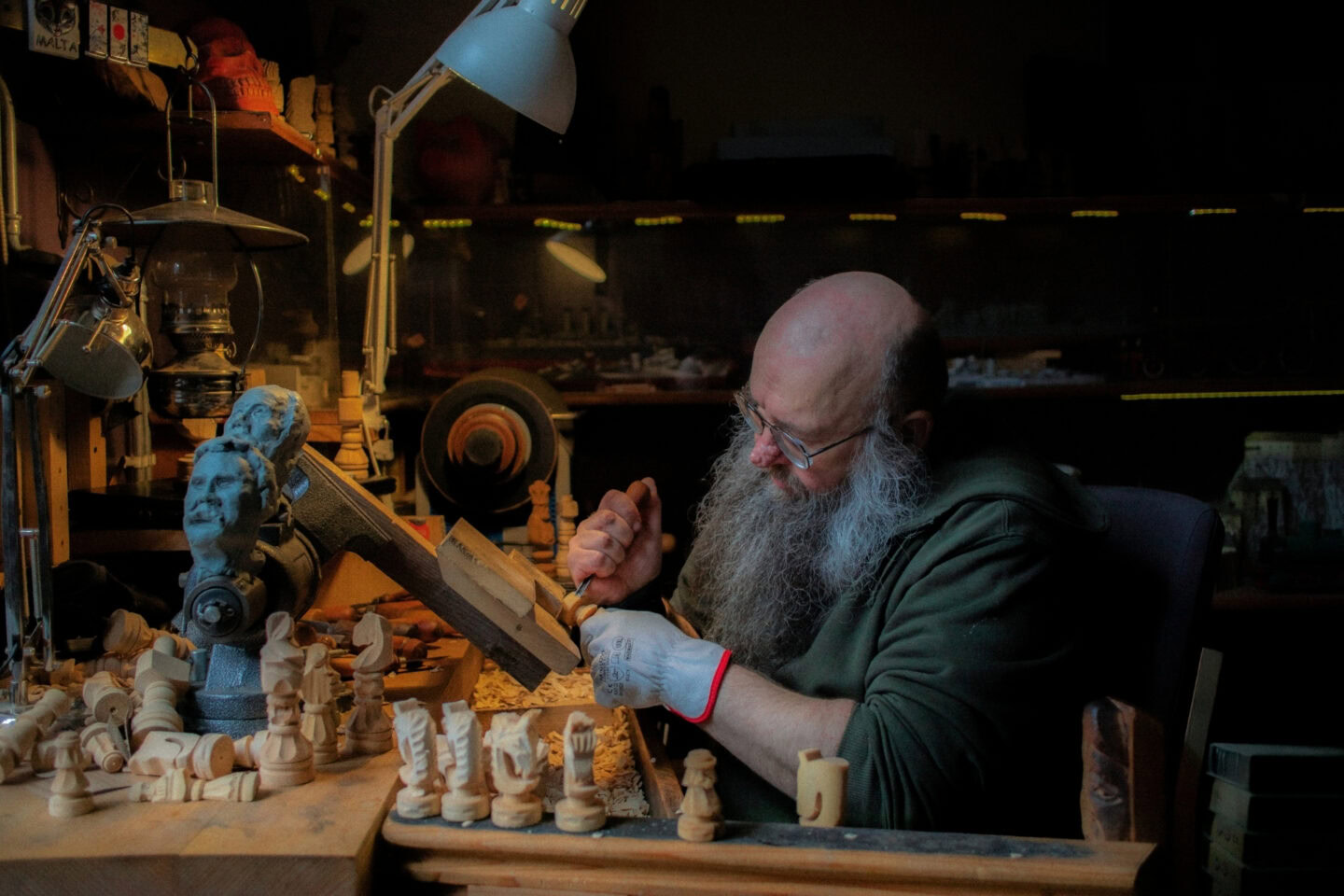
PK: How many such already developed models can be made in a day?
It once happened to me that I made probably five or six sets in a day - it was an urgent order and I worked very long hours to meet the deadline. This is probably my record, but it is not realistic to work like this every day, even if these were quite simple models. I remember that the next day my wrist hurt so much that I couldn't even do one set. Now I avoid such situations and make sure not to overload my wrist, because it is my work tool.
PK: Let's assume that someone comes to you today and wants to order a chess set - one of the models that you have already developed. How long a waiting time are we talking about in this case?
It depends on what stage of production I am at. If I have stamped wood for this particular model in my workshop, the waiting time is usually between a week and a week and a half. If I don't have pre-embossed elements, things get more complicated. In the case of individual orders, it is a completely different matter and the waiting time is definitely longer.
PK: So what does working with individual orders look like?
Sometimes it is a matter of personalizing an existing model, e.g. by replacing or modifying one type of figure. Now I am working on such a mixed set, where only the figure of the jumper will be changed from a horse to a Schnauzer dog.
When it comes to individual orders, the biggest challenge for me as a creator is not to overdo it with the amount of detail and perfectionism, because such projects could actually be refined endlessly. When creating any object, whether it's a carved chess set, a painting or something completely different, at some point you have to decide that the work is ready.
PK: Customers can visit you in the workshop and they will probably ask many questions about the process of making such chess sets. Are there any issues that often surprise customers?
One thing that most people don't know is that when carving such chess pieces, I first soak them in water. Some harder types of wood, such as oak or cherry, I usually boil before I start carving them. This makes the wood softer and easier to work with. It is important to dry the soaked wood later at the appropriate temperature, otherwise cracks will appear and the work will be wasted.
Customers are often not aware of the limitations associated with working with a material such as wood. They are often asked to create a custom design that is full of details despite its small size. This is often due to the fact that they see something on the Internet without knowing the size of the product whose photo they are looking at. Later, it often turns out that when they looked at, for example, 30-centimeter figures, they believed that they were looking at a standard-sized chess set.
Another issue that I often explain to clients is how much influence the choice of a specific type of wood can have on the price of the final product - this is not only due to the price of the raw material itself, but also how to work with it and what impact it has on working time.
PK: Apart from wood, are there any other materials that you work or have worked with?
Yes, I'm starting to experiment. For example, I created chess pieces using resin. I'm thinking about making ceramic chess, so I'm testing the possibilities of working with clay. We'll see what comes of it. Sometimes ideas for using new materials appear somewhere. Some time ago, while walking around the quarry, it occurred to me to try carving something in the stone. I brought various stones to the workshop and tested what I could do with them. It turned out, as you probably guessed, that one stone is not the same. Sometimes nothing came out and sometimes I carved the material quite well and I really liked the effect. But for now, these are just ideas - you can't do everything at once. Unfortunately, there are a limited number of hours in the day.

PK: You have been creating your own carved chess pieces for over 20 years. Is there anything that has changed during this time?
Definitely. First of all, people increasingly appreciate the fact that my products are handmade.
Chess pieces can also be carved digitally, in a very mechanized way. These digitally carved chess pieces can have a lot of detail. Today, technology allows the production of figures with very complex shapes, regardless of their size. However, these are mass-produced products, although in theory carved. They all look identical and lack the authenticity that is inherent in craftsmanship. In times of mass production and ubiquitous low-quality, almost disposable products, people increasingly appreciate items that are made by hand. I have the impression that what used to be a delight as a new technology just entering the market has now become a bit boring for the recipients. This is a big change. When I started carving chess, it was completely different. Back then, customers were more likely to choose digitally carved products, now they prefer to choose those that are more unique.
PK: What drives you as a craftsman?
For me, what is most important is that my work gives me pleasure.
PK: Could you give some advice to young people who, like you, would like to pursue something creative professionally?
Yes, above all, it is important not to give up when something doesn't work out at the beginning. We know that it is not a pleasant feeling when we try and try and something fails. In such moments you cannot immediately break down and give up these attempts. It's worth being positive, sometimes it's just a bad day or the fact that we put too much pressure on ourselves. Instead of feeling down, it's better to take a break and think "maybe tomorrow it will work" and keep doing it until it works out. And if it doesn't work for us for a long time, maybe it's worth trying something else.

For a job like mine, you often need a lot of patience and persistence in pursuing what you want to achieve. I think this is true of all creative professions.
It is certainly not worth approaching it with the thought that we will earn a lot of money from our creative work from the very beginning. Such work usually requires a huge amount of time and does not immediately bring us profits. In moments like these, we need to remind ourselves why we are doing this.
PK: At the end of our conversation, I would like to ask why, in your opinion, it is worth choosing handcrafted products?
Mainly because of its uniqueness. I would say that these items are not produced but manufactured. There is a subtle difference, even between these two terms. In my opinion, something that has been produced has been created once and there is no second such identical item. However, something that is produced is more associated with a production line, a repeatable, mechanized process that results in the same final products.
PK: Are some more difficult to make than others?
Each one is easy to make if you know how. Likewise, each one is difficult when you do it for the first time. When you don't have any form, you have to think and test different solutions.
PK: Do you also wear hats every day?
Oh yes! As always, I am the first to put on my hat when fall approaches and the last to take it off when spring comes.